压铸(die casting)是一种金属铸造工艺,其特点是利用模具腔对融化的金属施加高压,类似于塑料的注塑成型。压铸特别适合制造大量的中小型铸件,因此压铸是各种铸造工艺中使用最广泛的一种。同其他铸造技术相比,压铸的表面更为平整,拥有更高的尺寸一致性。然而,不规范的操作和参数也会产生种类众多的缺陷。
一、流痕和花纹
外观检查:
铸件表面上有与金属液流动方向一致的条纹,有明显可见的与金属基体颜色不一样的无方向性的纹路,无发展趋势。
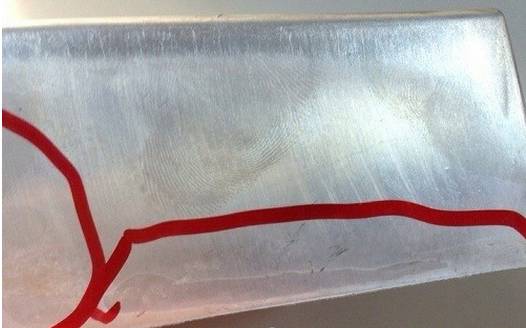
流痕产生的原因有如下几点:
- (1)模温过低;
- (2)浇道设计不良,内浇口位置不良;
- (3)料温过低;
- (4)填充速度低,填充时间短;
- (5)浇注系统不合理;
- (6)排气不良;
- (7)喷雾不合理。
二、网状毛翅(龟裂纹)
外观检查:
压铸件表面上有网状发丝一样凸起或凹陷的痕迹,随压铸次数增加而不断扩大和延伸。
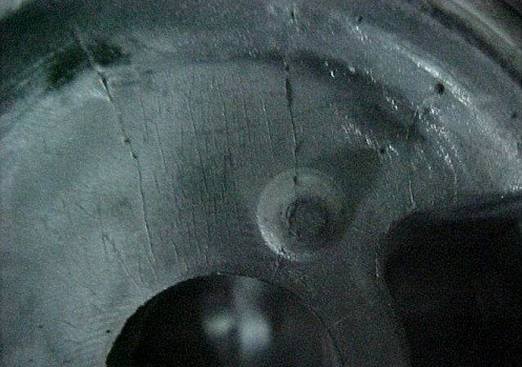
产生原因如下:
(1)压铸模腔表面有裂纹;
(2)压铸模预热不均匀。
三、冷隔
外观检查:
压铸件表面有明显的、不规则的、下陷线性型纹路(有穿透与不穿透两种)形状细小而狭长,有时交接边缘光滑,在外力作用下有断开的可能。
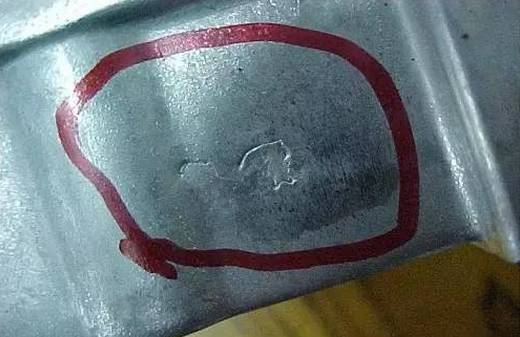
产生原因如下:
(1)两股金属流相互对接,但未完全熔合而又无夹杂存在其间,两股金属结合力又很薄弱;
(2)浇注温度或压铸模温度偏低;
(3)浇道位置不对或流路过长;
(4)填充速度低。
四、缩陷(凹痕)
外观检查:
在压铸件厚大部分的表面上有平滑的凹痕(状如盘碟)。
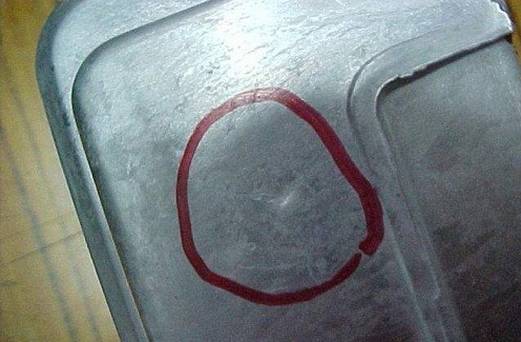
产生原因如下:
- (1)由收缩引起:压铸件设计不当壁厚差太大;浇道位置不当;压射比压低,保压时间短;压铸模局部温度过高。
- (2)冷却系统设计不合理;
- (3)开模过早;
- (4)浇注温度过高。
五、印痕
外观检查:
铸件表面与压铸模型腔表面接触所留下的痕迹或铸件表面上出现阶梯痕迹。
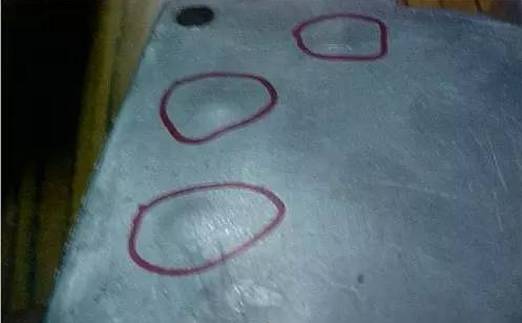
产生原因如下:
(1)由顶出元件引起
- 顶杆端面被磨损;
- 顶杆调整长短不一致;
- 压铸模型腔拼接部分和其他部分配合不好。
(2)由拼接或活动部分引起
- 镶拼部分松动;
- 活动部分松动或磨损;
- 铸件的侧壁表面,由动、定模互相穿插的镶件所形成。
六、粘附物痕迹
外观检查:
小片状及金属或非金属与金属的基体部分熔接,在外力的作用下剥落小片状物,剥落后的铸件表面有的发亮、有的为暗灰色。
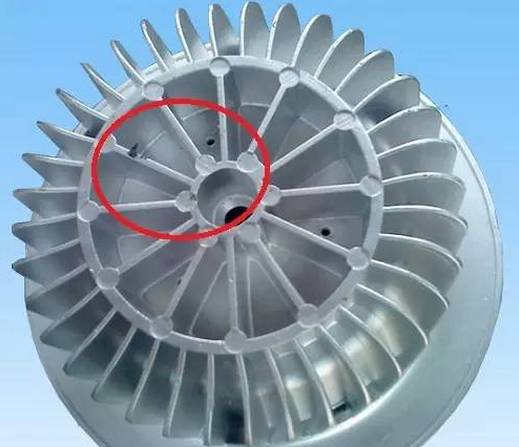
产生原因如下:
- (1)在压铸模型腔表面有金属或非金属残留物;
- (2)浇注时先带进杂质附在型腔表面上。
七、分层(夹皮及剥落)
外观检查或破坏检查:
在铸件局部有金属的明显层次。
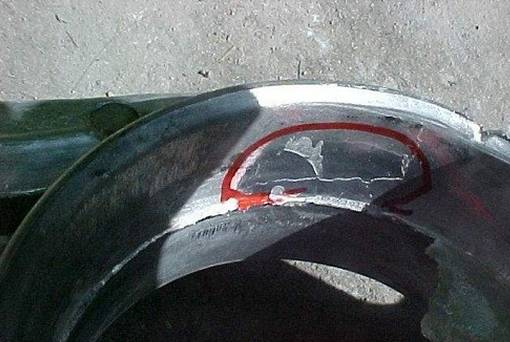
产生原因如下:
(1)模具刚性不够在金属液填充过程中,模板产生抖动;
(2)在压射过程中冲头出现爬行现象;
(3)浇道系统设计不当。
八、 摩擦烧蚀
外观检查:
压铸件表面在某些位置上产生粗糙面。
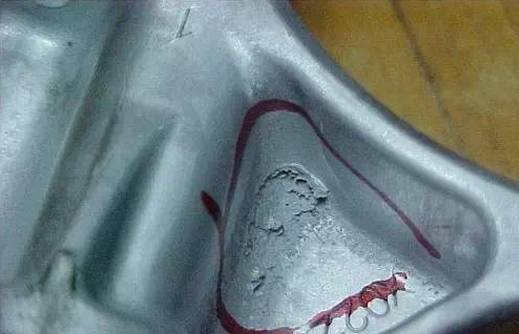
产生原因如下:
- (1)由压铸型(模)引起的内浇道的位置方向和形状不当;
- (2)由铸造条件引起的内浇道处金属液冲刷剧烈部位的冷却不够。
九、冲蚀
外观检查:
压铸件局部位置有麻点或凸纹。
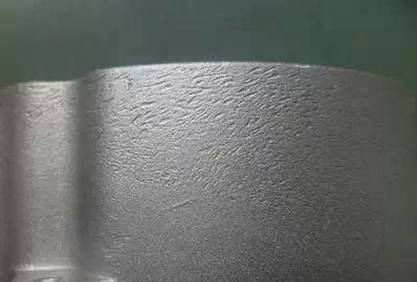
产生原因如下:
- (1)内浇道位置设置不当;
- (2)冷却条件不好。
十、裂纹
外观检查:
将铸件放在碱性溶液中,裂纹处呈暗灰色。金属基体的破坏与裂开呈直线或波浪线形,纹路狭小而长,在外力作用下有发展趋势。
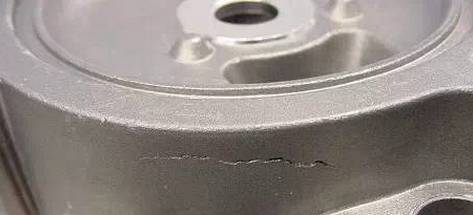
产生原因如下:
- (1)合金中铁含量过高或硅含量过低;合金中有害杂质的含量过高,降低了合金的可塑性;铝硅合金、铝硅铜合金含锌或含铜量过高;铝镁合金中含镁量过多;
- (2)留模时间过短,保压时间短;铸件壁厚有剧烈变化之处;
- (3)局部包紧力过大,顶出时受力不均。