《高效轧制国家工程研究中心成立二十周年系列技术报道》
通过多年的研究和实践,北京科技大学高效轧制国家工程研究中心成功开发出具有全部自主知识产权的一系列全流程板形控制技术及核心工艺,使板形控制的技术指标达到国际先进水平,并且形成了一整套包括机型、辊形、工艺、控制、管理在内的全工序板形综合解决方案,使板形质量得到有效控制,实现了板形综合控制技术从消化吸收、创新到引领的新高度。
板形是板带生产过程中的重要质量指标,由于影响因素多,生成机理复杂,且各影响因素之间还存在不确定、非线性、强耦合的关系,因此,板形控制一直是板带生产过程中的热点和难点。新世纪以来板带轧机的建设进入了一个新的高潮。以钢铁企业热连轧机为例(包括常规和短流程工艺),据不完全统计,截至目前,我国已建、在建的1250mm以上轧机已经超过90套,且各钢铁企业均不断提升产品附加值,开发品种包括电工钢、镀锡板、汽车面板、高强度结构钢、不锈钢、高级别管线钢等。板形不仅是这些高端板带产品的重要质量指标,而且板形好坏时常会影响到轧制稳定性,进而成为生产能否顺行、产品规格能否突破的关键。
从板带轧制技术诞生开始,板形质量控制研究便随之展开。国外板形控制理论的研究起源于20世纪50-60年代,我国针对板形控制理论的研究在20世纪60-70年代展开,首先,基于基础理论对板形生成原理及控制技术进行分析,随后在板形仿真软件开发、辊形技术、国外板形控制系统的消化和优化等方面取得了较大进展。2002年,北京科技大学高效轧制国家工程研究中心(以下简称轧制中心)率先开始了全套板形控制系统的自主研发,通过后续不断优化和推广,打破了国外在宽带钢板形控制系统方面的垄断,并在板形质量控制方面取得了理想效果。
板带生产是典型的流程工业,近年来,随着市场标准的不断提高,越来越多的实践表明,板形质量控制更应从全工序出发,结合设备、工艺、控制及管理,方可得到稳定的板形质量。经过多个全流程板形控制实践,形成了从理论到实践、从单工序到多工序的一整套板形综合解决方案,从而达到了板形技术从消化吸收到创新,再到技术引领的新高度。
1. 板形控制理论的发展及创新
经过20多年的持续研发,在板形控制理论方面取得了创新性的理论成果,具体内容包括:
- 1)提出了二维变厚度有限元模型和快速辊系变形方法,在求解速度和精度上均达到较高水平,并成功通过了国内多套连轧机的在线精度检验。轧件变形方面,基于合理假设及渐近计算原理,采用有限体积法建立带钢三维塑性变形模型,实现了轧辊轧件变形的快速耦合求解。
- 2)考虑复杂边界条件,建立了基于显隐交替差分格式的轧辊温度场模型和基于快速有限元的轧辊热变形模型,实现了对工作辊瞬态温度场和热辊形的精确预报。
- 3)提出了多工况下的工作辊磨损预报模型,能准确量化润滑轧制、高速钢轧辊等对磨损的改善作用,采用模拟退火遗传算法等智能算法确定模型关键参数。
- 4)利用有限元二次开发功能,建立了温度-相变-应力应变一体化耦合模型,实现带钢轧后冷却过程中板形演变的耦合求解。
2. 先进辊形技术的自主研发
板形控制技术的每次飞跃,总是来自于轧制设备结构的革新及工艺思想的升华,如液压弯辊技术的出现,使得板形控制不再单纯依赖轧机负荷分配及初始辊形配置,为板形控制提供了直接、高效的调节手段,实现了板形质量第一次质的飞跃;液压窜辊技术的出现,推动了轴向移位变凸度类工作辊技术的不断发展,提供了更为强大的板形控制能力。实现了带钢断面质量和浪形的协调控制;提高横向刚度和减少有害接触区思想的提出则衍生出了大量新轧机机型和先进轧制技术,如HC轧机、UC轧机、变接触轧制技术等。轧制中心在辊形技术方面进行了大量研究,开发出了一系列先进的辊形技术。
2.1 高效变凸度工作辊辊形技术的研发
三次曲线工作辊辊形目前在轧制过程中已经得到广泛应用,其板形控制能力随着带钢宽度的变窄成平方关系下降。为了增大轧机的板形控制能力,尤其是增加轧机对窄规格带钢的板形控制能力,开发了高效变凸度辊形(HVC),实现了等效凸度与窜辊位置成线性或近似线性关系。HVC辊形使得辊缝在指定宽度区间内呈线性化,而在其他宽度区间内呈二次函数平滑分布,保证工作辊的等效凸度调节能力满足各种宽度规格带钢板形控制的需求。
2.2 变接触支持辊辊形技术的研发
热轧轧制条件复杂恶劣,板形控制的干扰因素很多,所有干扰因素可集中表现为轧制过程中轧制力的波动和辊形的变化,为了消除或减轻轧制力的波动和辊形的变化对板形控制、操作等造成的影响,改善轧机的板形控制性能,轧制中心开发了变接触支持辊技术(VCR)。
此技术的核心是在支持辊上磨削特殊的辊形曲线,使得辊系在轧制力的作用下,支持辊和工作辊的辊间接触长度能够与所轧带钢的宽度相适应,减少或消除辊间有害接触区,提高承载辊缝的横向刚度,增加轧机对板形干扰因素(包括来料的板形波动和轧制力波动等)的抵抗能力,抑制板形缺陷的产生,使轧后带钢的板形保持稳定。
随着HVC/CVC等轴向移位变凸度工作辊的广泛使用,轧制中心又开发了新一代变接触支持辊辊形技术(VCR+),通过设计原始的变接触支持辊曲线,并在此基础上叠加高次工作辊曲线,达到提高变接触轧制效果的目的。图1所示为VCR+和高次曲线工作辊的配合情况。
图1 VCR+支持辊和高次曲线工作辊的配合
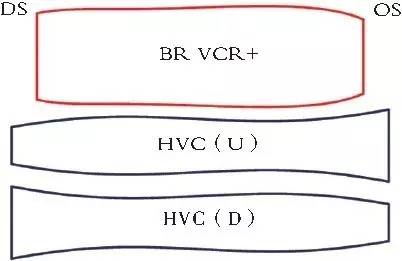
变接触支持辊可以将低横向刚度的辊缝转化为高横向刚度的辊缝,显著提高轧机的板形控制性能。VCR/VCR+技术改变了支持辊与工作辊辊间的接触状态,对改善支持辊轴向不均匀磨损具有积极的作用。
自20世纪90年代变接触支持辊技术开发成功以来,变接触支持辊技术在国内各大钢厂的热轧、冷轧、平整得到了大量应用,在防止轧辊剥落、降低辊耗、延长轧辊服役周期等方面均取得了良好效果。此外,VCR/VCR+技术以及HVC工作辊辊形技术还成功输出到韩国浦项光阳四号热连轧生产线。
2.3非对称工作辊辊形技术的研发
随着市场多钢种、小批量及交叉轧制的需求不断增加,传统的棺形轧制计划编排原则也越来越难以实现;同时,低凸度、超平材的需求也被市场所提及。CVC、HVC等轴向变凸度工作辊主要用于控制带钢宽度方向辊缝形状,这类辊形在轧制过程中的磨损特征与常规凸度工作辊相同,但由于其窜辊是根据轧制带钢各道次的目标板形进行设定,不但无法做到均匀化磨损,而且当磨损累积到一定程度以后,辊形原有的控制特性也很难保持。为了满足以上控制需求,轧制中心开发了非对称工作辊辊形技术(ATR),其设计思想是利用辊形和窜辊的非对称性来改变工作辊的磨损特性,进而改善辊缝的非对称性。
图2为ATR辊形的工作原理,根据轧制过程中轧辊的磨损规律,设定特殊的窜辊方式,使得工作辊的磨损由凹槽形转化为半开放形磨损,即打开凹槽一个边,使带钢始终处于辊形较为平坦的区域内,打破由宽到窄的棺形轧制规程约束,并结合强力弯辊保证承载辊缝的正常可控。ATR技术在一定程度上可以实现自由规程轧制(SFR),同时由于其一端带有锥形,一方面可以提高弯辊力的作用效果,减小有害接触区,提高辊缝横向刚度;另一方面,锥形部位可以对带钢边部产生局部作用,显著改善带钢边部板形,能满足硅钢等专用钢对边部板形控制的特殊要求。
图2 ATR工作辊设计示意图
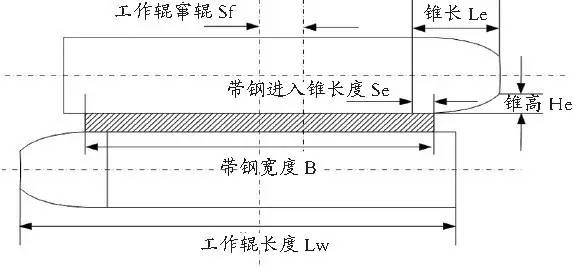
2.4冷轧边部变凸度工作辊辊形技术的研发
冷轧硅钢作为国家优先发展的高效节能的优秀软磁功能材料,是我国钢铁工业品种结构调整的重中之重。冷轧硅钢最终要进行叠片,因此对同板差的要求非常高,目前市场的准入条件为同板差小于10μm,高端市场则接受7μm以下。冷轧硅钢同板差控制瓶颈主要在于边部减薄,而边部带锥度工作辊的使用是冷轧带钢边部板形控制的重要手段。如果冷轧机工作辊带窜辊,如UCMW、HCMW轧机,则可以在工作辊上设计简单锥度,通过边降控制仪检测到的带钢实时边降值调整窜辊,做到边降闭环控制,得到较好的精度;而对于一些工作辊不能窜辊的冷轧轧机,则初始辊形设计对于边降的控制具有积极的意义。轧制中心提出了边部变凸度工作辊(EVC)技术,主要用于冷轧轧机,实现在一个轧制单位内,宽度带钢近似相同情况下的冷轧带钢边降控制,如图3所示。
图3 EVC工作辊设计示意图
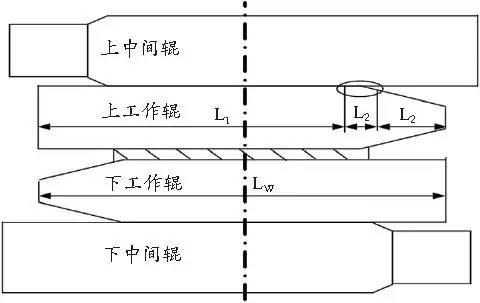
2.5混合变凸度工作辊
混合变凸度工作辊(MVC)主要用于解决热轧过程中的高次浪形,其开发需求来自于热轧不锈钢的四分之一浪。
热轧不锈钢轧制过程有两大明显特点:
- 1)温降大。如果没有边部保温或边部加热等措施,热轧不锈钢精轧出口横向温差经常能够超过100℃;
- 2)负荷大。相比于同规格普碳钢,不锈钢的负荷更大,特别是低镍高氮类不锈钢,负荷能增加70%-90%。
在采用1450mm、1580mm、1780mm热轧轧机进行不锈钢生产时,精轧出口会有明显的高次浪形缺陷,主要表现为双侧四分之一浪形,而且对于固定宽度轧机,四分之一浪的位置也相对固定。为此,轧制中心开发出一种特殊的工作辊辊形,对于特定的轧机,在四分之一浪出现位置相对固定的前提下,在出现浪形区域,对辊形进行适当的补偿,通过辊形的补偿减小局部压下量,避免浪形的发生。如图4为MVC工作辊辊形对高次浪形的补偿示意图。
图4 MVC工作辊辊形对高次浪形的补偿示意图
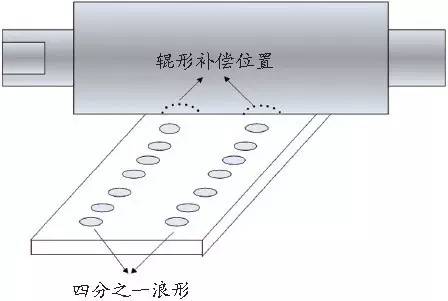
3. 高精度板形控制系统的国产化进程
长期以来,能开发全套板形控制模型的只有国外少数电气公司,国内多家科研院所从20世纪60-70年代开始,也在板形理论领域进行了深入的研究,并取得了一些成果,但从理论研究到现场运用,特别是成套板形控制系统的工业运用一直未有起色,同时,外方对板形模型的关键技术封锁愈加厉害,企业在后续维护以及产品扩展方面显得力不从心。
近20年,轧制中心在板形控制理论及板形单项技术上进行了大量研究,基于理论研究的板形离线仿真模型也相继被开发出来,并着手于在线板形控制模型领域内的进一步开拓,开拓初期遇到诸多困难,归结为以下几个方面:
- 1)缺乏具有自主知识产权的过程控制平台。国内早期对引进的热轧过程控制系统进行了一些消化和吸收,但自主开发成套的过程控制系统还是近些年才得以实现,作为全线控制系统的一部分,板形控制模型同样需要这个平台,进行如数据交换、事件触发、进程通讯等工作,因此,自主板形控制模型的开发在周期上存在对平台的依赖性。
- 2)缺乏实体对象。国内早期的热连轧走全盘引进的路线,国内研究机构很难有机会参与过程控制系统的建设,虽然轧制中心已较早开发出板形离线模型,且在一些试验轧机上进行了相关验证,但由于基于理论的离线模型和在线模型之间必然存在一定的差别,为保证模型精度,需要对一些参数进行在线修正,对于一些异常事件的处理也需要通过在线方式得以发现,因此,具体的轧机对象在模型开发过程中非常重要。
- 3)板形相关工艺有待于进一步探索。板形控制与厚度控制、温度控制等最大的不同点是板形与现场工艺结合紧密,在从无到有的研发过程中,模型和工艺之间如何紧密结合尚需进一步的探索,探索过程主要是现场跟踪、模型优化、再跟踪、再优化这一反复过程,后续的模型开发也证明了这一内容的重要性。21世纪以来,随着宽带钢热连轧的国产化进程加速,板形控制系统的自主研发也引来了契机。
板形控制的主要控制目标有凸度控制、平坦度控制以及局部断面形状控制,轧制中心开发的板形控制模型简称PFEC,其功能如图5所示,P代表凸度控制;F代表平坦度控制;E代表局部断面形状控制,主要指边降和局部高点控制。PFEC控制系统由两部分组成,分别为在L2实现的板形设定计算模型和在L1实现的动态板形控制模型。板形设定计算模型主要保证带钢头部,仪表检测到带钢前的板形质量,而动态板形控制模型主要通过板形实测值和外界因素(如轧制压力)的周期变化进行动态板形调节,保证带钢全长板形质量。
图5 PFEC板形控制系统功能框图
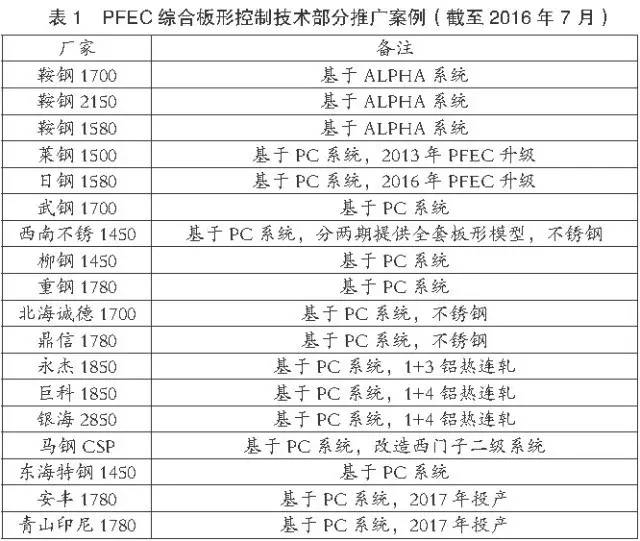
经过不断优化和升级,自主开发的全套板形控制模型(PFEC)不断推广到国内一些新建或改造的热连轧生产线,为企业带来了巨大的经济效益。截至2016年7月,PFEC板形控制模型推广案例见表1所示。
4. 全流程板带板形综合控制技术
板形控制技术一直是板带生产过程中的热点和难点,新设备、新工艺、先进控制系统也围绕着板形控制的需求不断涌现。客户对板形质量的反馈虽然一般来自于最后工序,但由于在整个板带生产过程中,工序与工序之间有着密切的联系,上游板形质量直接关系到下游来料的初始板形,因此,只在单工序进行板形质量控制难以取得理想的效果。众多企业开始意识到,仅在局部流程进行技术攻关和研究并不能解决最终的质量问题,而需要各个工序配合,从技术上、流程上、管理上进行统一考虑。在板带生产流程中,和板形控制相关的工序主要有加热、热轧、层冷、冷轧、退火、平整等,这也决定了如果想得到良好的板形质量,需要研究上述工序对板形的影响机理。板形控制技术由于涉及到设备、控制、工艺、管理等一系列过程,影响因素多,基于此,轧制中心率先在国内提出全流程板形控制的理念和思想,开发了一系列的板形控制技术及核心工艺,并在宝钢梅山、马钢、涟钢、新钢、邯钢等多个企业得到成熟应用,归结如下:
- 1)高品质用钢的起筋控制技术。通过研究起筋机理,从热轧工序、冷轧工序、连退工序、镀锌工序中分别找出可能导致起筋的关键因素,然后综合采用断面控制技术、水系统管理、冷轧目标曲线优化、退火温度控制、卷取张力控制等手段,实现高品种用钢冷轧工序中部起筋和边部起筋的有效控制。
- 2)硅钢全流程板形控制技术。通过在热轧工序、冷轧工序、平整工序进行相应的研究,采用热轧工作辊辊形技术、冷轧工作辊辊形技术、平整辊形配置技术等,实现不同类型轧机的硅钢板形控制,包括高精度断面质量控制及浪形控制。
- 3)板形质量综合解决方案。通过对大量板形质量异议进行分析,辅以先进数据挖掘技术,从温度控制、班组管理、模型精度、辊形设计、平整工艺等多个环节,提出一整套板形质量异议的解决方案。
- 4)轧后板带内应力减量化技术。基于ABAQUS有限元建立热轧带钢在不同冷却工艺条件下的有限元模型,实现温度、相变、应力三者的耦合计算,并进行温度测试、材料微观组织测试、应力测试等多个试验验证,得到轧后层流冷却过程中,内应力演变规律和减量化手段,对分析带钢轧后冷却不均、应力不均、翘曲等具有重要意义。
5. 结论和展望
通过20年的研究和实践,轧制中心成功开发出具有全部自主知识产权的成套板形控制技术,申请国家发明专利超过20余项,获得国家科技进步奖1项,省部级奖励6项,使板形控制的技术指标达到国际先进水平,并且形成了一整套包括机型、辊形、工艺、控制、管理在内的全工序板形综合解决方案,实现了板形综合控制技术从消化吸收、创新到引领。
展望未来,板形控制模型和相应工艺仍然还存在需要完善和改进的地方,特别是镰刀弯的检测及控制技术、薄规格轧制浪形控制技术、模型对换规格的适应性等还有非常大的提升空间,对检测技术的研究,对设备精度状态的数字化评价、监控及维护将是板形控制面临的最大挑战。
作者:邵健
来源:本文摘选自《世界金属导报》2016年第35期B08。