作者:李岩
一、Moldflow在企业的长期应用效益分析
1.筋位设计优化效益
柜口原始产品筋位设计过高,从客户的使用功能上看防发泡溢料的筋位高度在10mm左右就可以了。筋位优化后制品重量可降低30g左右,且筋位的抱紧力减少,优化制品现有筋位拉白问题,同时可降低成型压力。
效益分析:制品筋位和壁厚优化后制品重量单件可降低重量100g左右,按冷柜柜口所有型号年产30万算,一年可节省57万。
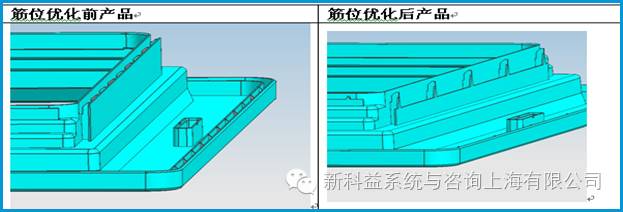
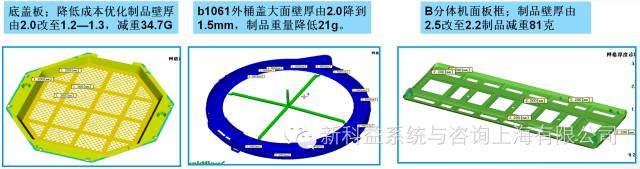
2.浇注系统优化效益
内桶底:浇注系统由热流道四点直浇口改为冷流道缝隙浇口,可降低模具成本50000,生产节拍缩短20S。按年产50万算,一年可节省17万。
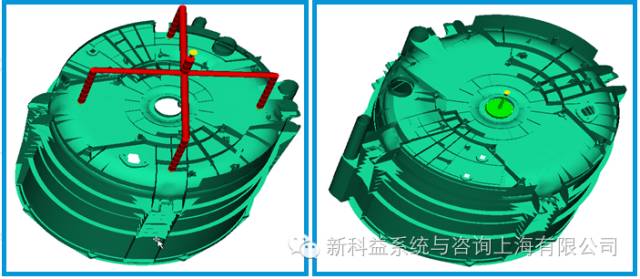
控制盘座:通过优化按钮悬臂梁尺寸,按钮上不需要放置浇口可成型,浇注系统改成热流道减轻料把重量50g。
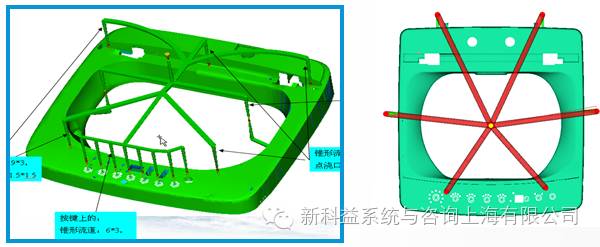
滤尘网:三板模点浇口改热流道点浇口,单件可省料把30g,周期提效5s。
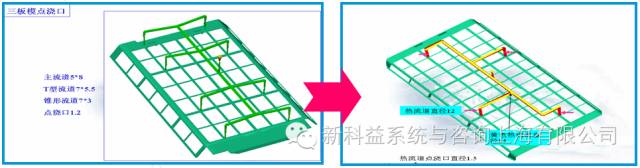
压机盖板:注塑机吨位不变,一模出两件。年可节约注塑成本20万。
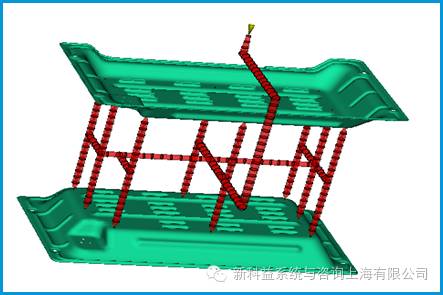
3.冷水水路优化效益
通过优化冷水水路,模具热点处镶铍铜。周期优化至65s左右。提效15S。按年产50万算,一年可节省12.5万。
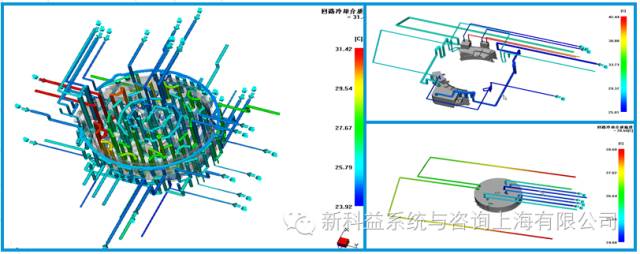
保险杠:优化周期13s。
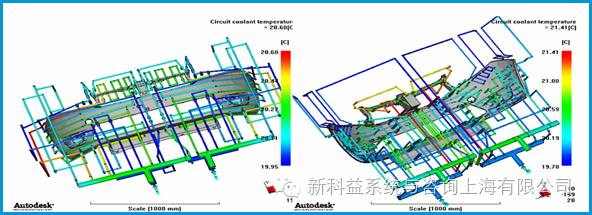
热水器前壳:周期可控制在50s,提效5S。
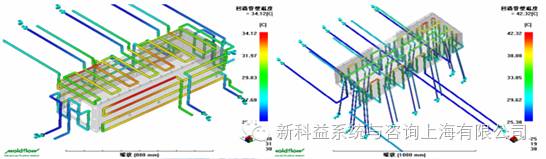
仪表板本体:热点优化可提效15s
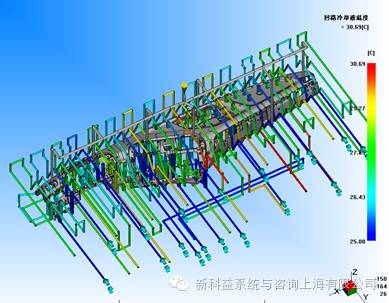
二、moldflow应用经验
1.变形
运行moldflow分析,变形的准确率可以在85%以上。通过分析可以提前预测产品的变形量,提出更改方案。避免了后期因为产品变形导致的大量修模问题。
2.气痕
(1)筋位冲出气痕
筋位排气不良,产品表面冲出水花。筋位根部加排气,或者更改产品造型使筋位根部不困气(筋位加厚或者倒大圆角。)
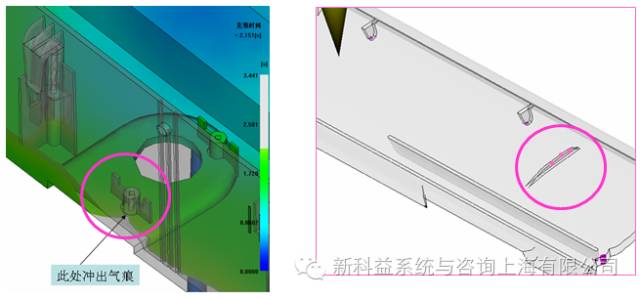
流经筋位的熔胶先达到侧壁,会在侧壁上筋位正对位置有气痕缺陷。改善方案产品壁厚调整或筋位造型优化。
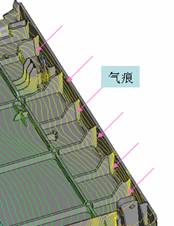
(2)产品造型导致气痕
浇口放置在红色箭头侧,熔胶从产品内侧往外冲,黑色箭头正对位置有气痕缺陷。升高模温可改善。
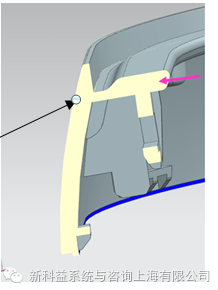
产品表面刻字或者造型凸起导致气痕。改善方案,刻字高度需控制在0.5mm以下。
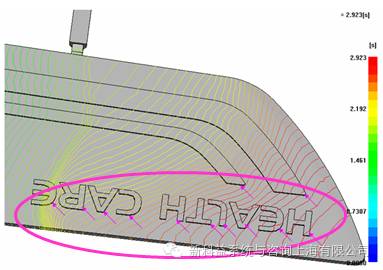
3.计算大型产品的锁模力
- (1) 在进行大型产品的CAE分析时,如何给出正确的锁模力是我们在日常分析中比较头疼的问题。
- (2) 锁模力=型腔压力*产品的投影面积,如何确定型腔压力是锁模力分析是否合理的关键。因此保压压力不能过大,如果过大将导致型腔压力较大,进而导致较大的锁模力。
- (3) Moldflow默认保压参数是成型压力的80%,大型产品的分析成型压力如果偏高,保压压力势必较高,导致了较高的锁模力。因此大型产品分析时需需综合考虑现场工艺条件,按照实际工艺条件合理设置保压压力,才能得到合理大小的锁模力。
三、Moldflow在海尔模具的应用案例
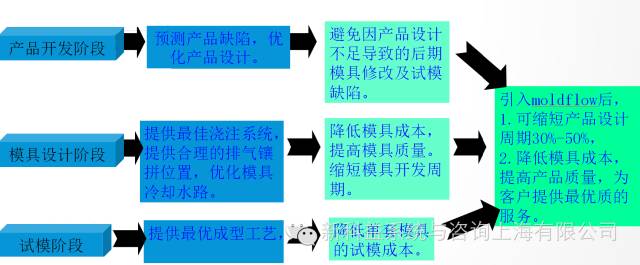
案例一:Moldflow在由变形导致的修模中的应用
商用空调接水盘,材料耐候ABS,主壁厚3.0mm。外形尺寸为1510 mm×291mm×276mm
客户要求:
- (1)销孔处(红色圆圈处)轴心处偏差需控制在0.5mm以内,
- (2)主装配边(红色线条标识处)变形需控制在2mm以内。
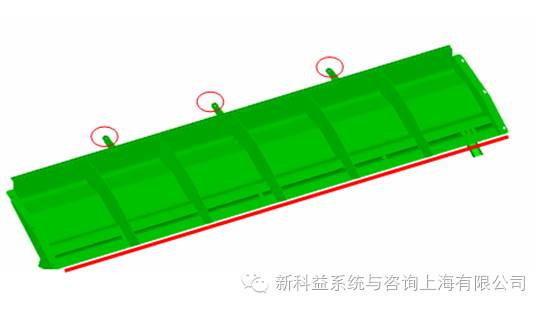
1.开模分析结果与试模结果对比
开模前分析结果:产品出模方向的变形量非常小,可以满足客户变形要求。
但是产品首试结果却大大出乎我们的意料。装配边的变形非常大约为8mm左右,销孔处轴心偏差大根本无法装配。通过现场工艺调整,无法得到满意的产品。需CAE查找原因并分析解决方案。
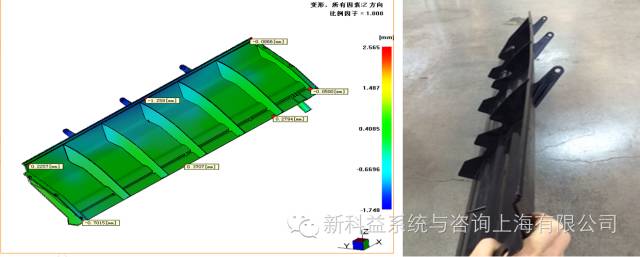
2.分析与实际变形不符原因排查
原因排查:
- (1)试模工艺,试模材料,冷却水,及浇注系统排查,无异常。
- (2)实际产品数据与分析数据对比,发现局部造型不一致主装配边处壁厚加厚(最厚处约为4.8mm),与分析数据不一致(如图4),是导致变形的主要原因。
采用最终数据运行CAE分析后我们发现变形分析结果与样件一致,如图5所示,因此产品局部壁厚加厚是导致产品出模方向变形加大的主要原因。
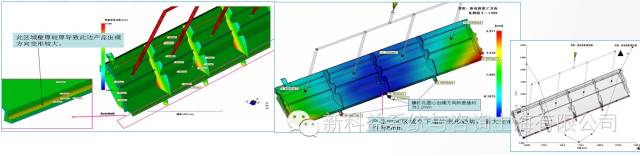
3.变形改善方案
塑胶件产生变形的原因是因为收缩不均产生的应力超过产品的刚度或者屈服强度后引起的变形。为此在不改变现有浇注系统,尽量减少模具改动的前提下。我们需要从增加产品刚度(加筋)或者减小产品上区域之间的收缩不均(调整壁厚)两个方面入手,来改善变形。
空调接水盘变形改善方案一:通过加筋来增强产品刚度
- 通过加筋来增强产品刚度,增强产品对抗变形的能力。
- 由分析结果知产品加筋后,主装配边的变形由8mm减小至4.8mm左右,确有改善但是远远达不到客户要求。同时因为加筋需要电火花加工,改模费用高,时间长。因此我们考虑采用减小收缩差异(调整壁厚)的方法来改善变形。
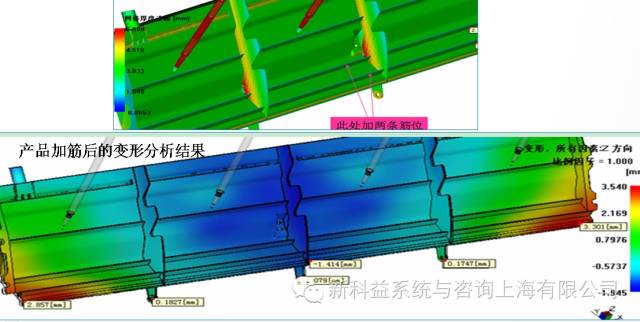
空调接水盘变形改善方案二:调整产品壁厚分布降低收缩差异来改善变形
通过调整产品壁厚分布,降低收缩来改善变形。
- 从浇口处加辅助流道:加强主装配边的保压压实,减小此区域的收缩,进而减小与大面的收缩差异。
- 产品靠近主装配边附近的大面壁厚加厚,通过减小壁厚差来减小由壁厚差异而改善收缩差异。
- 通过分析结果,产品壁厚优化后,变形可以满足客户要求。
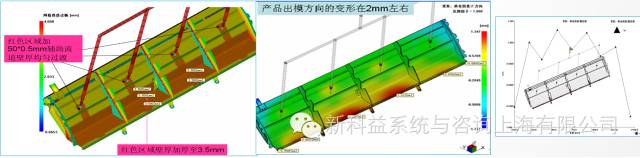
4.试模验证
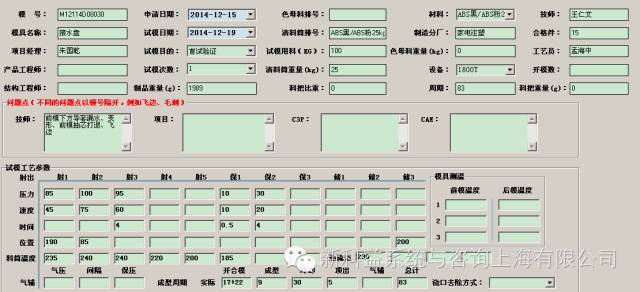
模具按照CAE优化方案更改后,试模产品的变形满足客户要求,销孔处于的变形非常小,装配时销钉可以一插到底。满足了客户要求,收到客户好评。
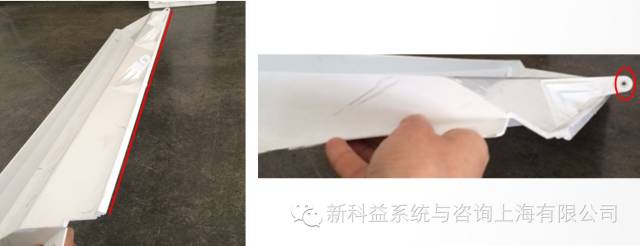
项目总结
- (1)CAE在注塑产品的变形分析中有着重要的指导作用,若实际试模结果与分析不一致,CAE工程师遇到这种问题首先需进行原因排查找出原因,并提供尽量简单易于实现,且更改成本最低的修模方案;
- (2)模具工程师在模具的制作过程中,特别是变形要求严格的产品。若产品更改必须将最新产品发给CAE重新运行变形分析,以确保分析数据的准确性;
- (3)产品的收缩导致的变形可通过增加产品的刚性及调整产品壁厚分布来改善。具体实施需要综合考虑成本及方案的可行性。选择模具更改最少,成本最低的改模方案;
- (4)开模前,通过CAE分析提前预估产品变形及其他缺陷。可避免后期这些缺陷导致修模。每套至少节约成本2500元,按照模具公司每年生产模具1000套计算每年可节约成本250万。
案例二:Moldflow在降低生产周期中的应用(异性水路)
波轮洗衣机波轮,材料耐候PP,主壁厚2.5mm。外形尺寸为344.5*344.5*77.5

1.原始设计方案
原始的模具水路设计:后模标识区域,筋位比较密集,是模具热点区域,受模具结构影响此处无法添加冷却水。
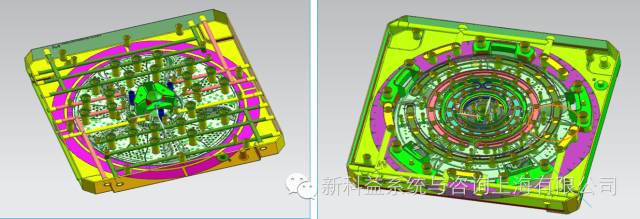
目前存在的问题:热点区域无冷却水,模温较高。导致产品冷却周期长,影响效率。
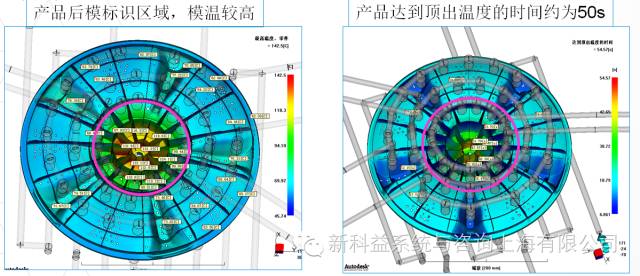
2.原因分析及改善方案
为了改善产品后模的冷却难题,我们采用3D打印技术,设计如下图所示的异形水路。
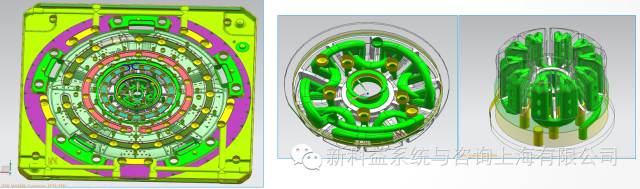
3.实际改善效果
添加异形水路后,热点处模温下降明显,产品冷却周期下降20秒。
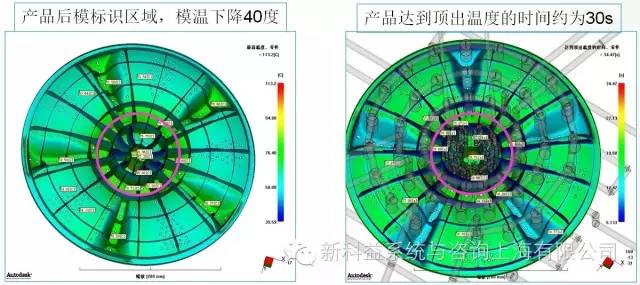
项目总结
- (1) 产品热点位置需要尽量添加冷却水。此产品热点处无冷却导致成型周期长,影响成本;
- (2) 添加异形水路后,热点处模温下降明显,产品冷却周期下降20秒;
- (3) 后模造型复杂的模具,水路设计完毕,需要进行冷却分析。提前预测热点位置,对水路设计进行修正。降低模具的冷却时间,降低生产成本;
- (4) 通过优化冷水水路,提效20S。按年产50万算,一年可节省12.5万。