模具是加工技术的核心。这些供应商通过减少模具、缩小模具尺寸、甚至采用逐层成形,不再使用模具等方法,既降低了成本,又保证了品质,非常值得我们借鉴。
一、Aqua成形法
从事除雪机开发和金属加工等业务的Fujii Corporation公司(总部:日本燕市新潟县),开发了减少模具费用的“Aqua成形法”,可实现深冲部件成形。Fujii公司已经将其应用到了农业机械联合收割机的部件加工中,生产脱谷作业中输送稻壳的风扇的旋转罩。材料选择的是厚2.3mm的深冲冷轧钢板(SPCE)。
Aqua成形法其实是“对置液压冲压成形法”的应用,采用了日本AMINO公司制造的对置液压冲压机。与通常的冲压机不同,在对置液压冲压机的主机下方设置了水槽,其中的水(或对置液)具有替代冲模承受冲压的作用。
使用Aqua成形法加工出的样品部件:首先,把钢板上取下的坯料成形为深冲形状。因为1次冲压即可完成深冲,所以可以减少模具。然后利用激光将其切割,涂装制作成样品部件。
这种冲压机首先需要使用二维激光加工机把钢板切割成需要的形状,然后将坯料设置在冲压机上冲压。此时,坯料上持续承受垂直方向均匀的水压(对置液压),可以加工出与凸模形状完全一样的部件。还能根据冲压的进给速度,对固定坯料边缘的力(压边力)和对置液压进行优化,实现比使用冲模的通常冲压加工更深的冲程。冲压工序只需1次。
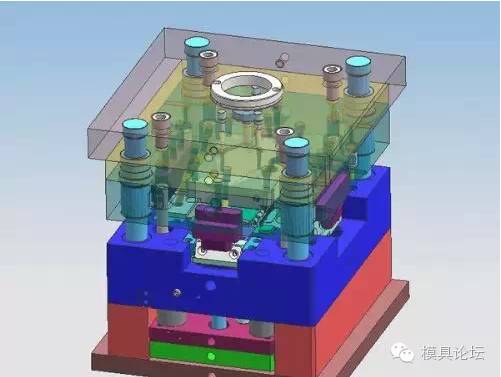
对置液压冲压机的构造:使用水(对置液)替代冲模。冲压坯料(工件)时,坯料垂直方向将承受均匀的水压(对置液压)。形成与凸模形状一致的深冲形状。
通过这一原理,Fujii Corporation公司只用1块坯料制,就能做出旋转罩。因为是一体成形,所以只需使用对置液压冲压机进行冲模。但在工件成形后,还要用三维激光加工机进行冲孔和切边。
过去,旋转罩分别使用普通冲压机制造两个部件,通过点焊和弧焊将其焊接在一起。其中1个部件需要3道工序,另一个需要5道工序进行冲压加工,也就是共需8个模具。
通过Aqua成形法,Fujii公司大幅削减了模具费,减少了部件成本。激光加工的成本则与过去焊接的成本相同。
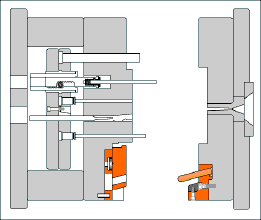
二、深冲难切削材料
加藤制作所(总部:岐阜县中津川市)也利用对置液压冲压成形法,实现了对难以进行机械加工的难切削材料的深冲。从而可以把不锈钢、钛合金、镍(Ni)基耐热合金“铬镍铁合金”和同样耐热、耐腐蚀的合金“哈氏合金”等特殊金属工件加工成具有深度的容器状,适用于飞机和医疗器械部件等领域。
难切削材料的深冲工件:把普通冲压机难以加工的不锈钢、钛合金、铬镍铁合金、哈氏合金等难切削材料的工件加工成为了具有深度的容器状。
例如,钛合金的加工硬化和回弹强烈,容易发生断裂。而且加工时,一旦表面的氧化覆膜剥落,钛合金就会与模具烧结,会损伤表面。因此在通常的冲压加工中,很难采用工件变形严重,加工硬化、回弹和模具烧结明显的深冲加工。虽然这个问题可以通过增加工序,使用逐渐改变工件形状的级进模,或涂抹加工油等方式解决,但耗费的成本太大。
而进行对置液压冲压成形时,承受冲压的是液体,与使用冲模相比,工件承受的摩擦小。这样一来,即使变形大,工件的表面也不容易出现裂纹,氧化覆膜也不易剥落。最终能够制造出没有破损和模具(冲压)烧结的高品质深冲产品。
因为只需要进行冲压,所以与使用复杂的级进模的普通冲压加工相比,也可以节省模具费。
三、仅更换腔体就足够
太阳五金制品公司(总部:日本堺市)通过缩小模具成功削减了成本。该公司开发出的“环保铸件”可以使用小于以往的模具,所以能够令采用切削、失蜡、铸造等方式加工而成的部件的成本减少60~70%。
使用小模具的“环保铸件”加工出的部件:通过替换利用切削、失蜡、铸造等方式加工的部件,成本可减少60~70%。
环保铸件的特点是把模具分成了共同的底座以及与成形品形状相同的腔体。在加工不同的部件时,底座作为标准品通用,只需更换腔体即可。而且,为了减少更换作业的麻烦,模具采用了卡带方式。打开顶板,把腔体插入到底座中即可完成模具设置。
环保铸件的模具:把模具分割成底座与腔体,加工时只需根据部件更换腔体即可。因为只需准备腔体的模具即可,因此模具费可以减少到约1/2
也就是说,环保铸件需要的模具只有腔体,材料只需传统模具的1至3成,加工时间约可减少1/2,模具费自然也可减少到1/2左右。而传统模具的底座与腔体合二为一,每加工一种部件都需要新模具,因此模具费偏高。
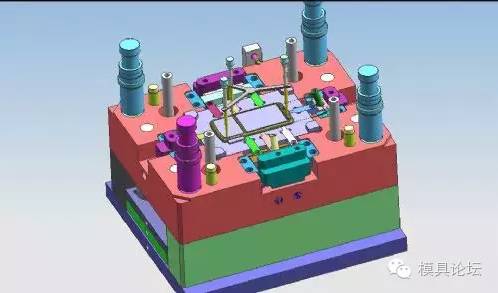
四、采用逐层成形,不再使用模具
无需模具即可加工复杂金属部件的技术也已经出现。那就是利用电子束的逐层成形(EBM)技术。其方式是向金属粉末照射电子束使其熔化,通过冷却凝固的方式加工复杂的金属部件。
KOIWAI(总部:日本秦野市神奈川县)引进瑞典Arcam开发的EBM装置,使用EBM技术加工了形状复杂的换热器。该部件与发电有关,网眼部分为散热片。网眼不仅精细,其中还配置了油管。因为使用温度高达数百℃,网眼部分与机壳的接合也无法使用焊接。
不使用模具制造的发电用换热器:成形借助的是使用电子束的逐层成形(EBM)技术。使用电子束照射铺设的金属粉末使其熔化,然后冷却凝固。通过多次重复这道工序,制成复杂的形状。
EBM技术能够根据三维CAD数据,直接对复杂的部件进行成形。EBM装置由电子束枪和反应室(成形室)组成。使用的金属粉末为含6%铝(Al)合金(重量比)、4%钒(V)的钛(Ti)合金Ti-6Al-4V,也就是“64钛”。
成形原理如下:首先,在反应室内铺设50μm厚的金属粉末。接着对部件形状需要的部分照射电子束。再在约1000℃的温度下,金属粉末熔化,照射电子束结束后,金属粉末重新凝固。之后再次铺设50μm厚的金属粉末,通过照射电子束重复金属粉末熔化和凝固的过程,逐渐制成了部件形状。加工速度为1小时8mm。制成换热器大约需要30个小时。
EBM技术的用途是加工研发使用的试制部件。有些构成高效率发动机的涡轮增压器和燃料喷射装置的部件试制项目,已经与KOIWAI公司进行了洽谈。因为这项技术能加工出此前无法实现的形状,所以“客户基本不问试制费要多少。虽然换热器的费用高达100万日元,但客户还是觉得‘便宜’。”(该公司称)
使用EBM技术加工的部件:面向研发的高单价试制部件众多。为了开发出高效率发动机,试制传统加工技术难以实现的复杂形状精密部件,存在着巨大的潜在需求。
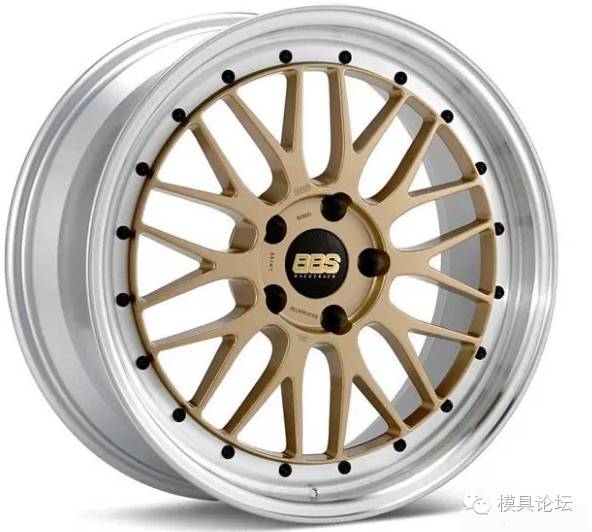
五、为模具追加组装功能
桥本精密工业(总部:东京)在模具内增加了组装功能。这家公司以钣金冲压加工为基础,开发出了在模具内进行成形以及组装的“模内一体组装”技术,并且利用这项技术加工出了汽车的滤油器部件。这种部件具有弹性,目前已作为固定纸制滤油器的部件投入实用。
汽车滤油器的部件:由钣金冲压成形的部件4层重叠组成。在4个部件中,2个部件的成形以及4个部件的组装是在模具(级进模)内处理。
滤油器部件由4个不同形状的部件重叠而成。其中,2个部件的成形与4个部件的组装采用同一个级进模。
具体方式是:沿级进模的纵向进给1条环箍材料,制成外盖。再沿垂直方向(横向)进给另一条环箍材料,制成内盖。然后再沿横向进给2条环箍材料。这2条材料已经通过其他工序成形了板簧和阀,与环箍材料一同进入级进模。
六、向滤油器部件的级进模进给的环箍材料
沿纵向向级进模进给外盖的环箍材料,沿横向进给内盖的环箍材料。这些材料经过冲压加工,制成外盖与内盖。而且,通过其他工序事先冲压形成了板簧与阀的2条环箍材料是沿横向向级进模进给。这些板簧与阀夹在外盖与内盖之间铆接。这项组装作业也是在级进模内自动完成。
在级进模内,板簧与阀夹在外盖与内盖之间,通过冲压把4个部件铆接在一起,制成滤油器部件。虽然还有其他可以在模具内组装部件的技术,但是要保证组装4个部件位置的偏差在5μm以内还是十分困难的。
以往,在完成冲压加工后,4个部件需要手工组装。现在在模具内完成组装作业,可以省去组装工序,降低部件成本。
七、使树脂与金属牢固接合
嵌件成型是指在配置于模具内的金属部件的周围注射树脂。为了使嵌件成型时金属与树脂牢固接合,ECO-A公司(总部:日本大船渡市岩手县)开发出了“通电加热式嵌件成型装置ELEBON PM-7”。在金属部件暴露的部分设置了与电极接触通电,在注射成形时进行加热的机构。
ECO-A开发的通电加热式接合装置:电极夹在表面经过了特殊处理的金属部件上下,通过通电对其加热。然后,通过挤压树脂部件使二者接合。通过为注射成形机配备该装置,嵌件成型的金属部件也能牢固接合。
金属与树脂接合的原理,即“化学偶联与锚固效应”。在金属部件表面,需要事先进行有机化合物三嗪硫醇表面处理。然后,在金属部件加热的状态下,以一定的压力把树脂挤压到部件表面,提高二者的接合强度。PM-7能够通过在树脂即将注射前进行加热缩短预热时间,借助电极直接冷却金属部件。
能够采用该技术接合的材料多种多样。过去需要使用螺丝固定的树脂部件与金属部件,如果能够在成形同时进行接合,就可以减少组装工时。设计方面,除了能够简化形状外,也有望实现低成本化,比如削减材料费。
来源:网络