中国模具工业协会DMC2016模具技术和设备评述专家组对DMC2016展出的各类模具、模具标准件及模具材料等展品进行了评述,介绍了我国模具、模具标准件、模具材料和模具 CAD/CAM/CAE 技术的发展现状和技术水平,分析了我国模具技术的发展趋势。
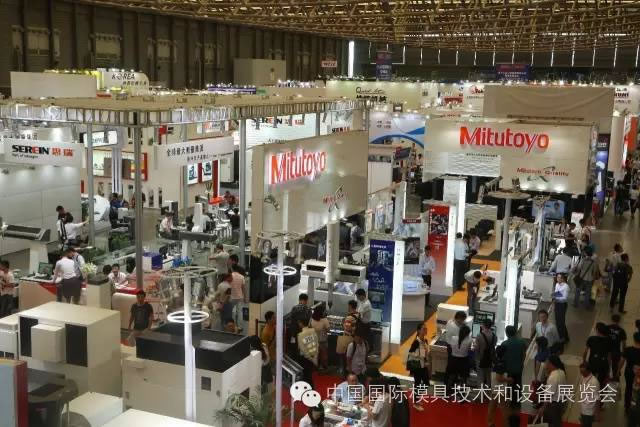
DMC2016是一届世界领先水平的先进模具、设备、技术与展览并举的国际化盛会,在展出的塑料模具、冲压模具、汽车覆盖件模具、铸造模具、模具标准件、模具材料、模具CAD/CAM/CAE、模具智能化以及互联网 + 等技术与产品中,有161副模具和10个标准件角逐“精模奖”,基本反映出了我国模具及其相关技术的发展状况与前沿水平,本文就塑料模具的技术及其发展水平进行评述。
一、 塑料模具篇
本届参展的塑料模具企业展出了两年来在技术创新、产品创新、模式创新方面的最新成果,模具行业的转型升级促进了塑料模具技术水平的提升,主要体现在 4 个方面。
1.塑料模具的智能化
模具智能化能够给模具用户提供最佳的使用体验,参展塑料模具企业在智能化模具技术的研发和应用方面有了较大突破,如模具型腔压力感知与反馈、模内在线感知系统等,能够把模具这个“黑匣子”里面的信息及时显示出来,为模具生产提供真实的塑料工艺数据,提高了模具工艺调试和生产的制造水平。因此,模具智能化相关技术的研发和应用将大幅度提升模具用户的满意度,具有广阔的市场前景,特别是在精密注塑件生产方面,可以更好地满足模具生产的高效率、高质量要求。
群达模具(深圳)有限公司开发的带有模内在线感知系统的注塑成型智能模具,安装有一种基于塑料介电特性的新型模内在线质量感知系统,对注塑过程各个阶段的关键质量参数进行在线实时检测。该模具的关键技术主要包括在线质量传感器的硬件设计与软件设计、高精度的电容信号测量与智能处理等。利用模具在线质量感知系统实现了注塑成型模具型腔内填充速度、填充压力、填充温度、填充时间、填充 V/P切换等综合工艺参数的实时在线感应、控制和优化,提升了注塑生产的效率和质量。
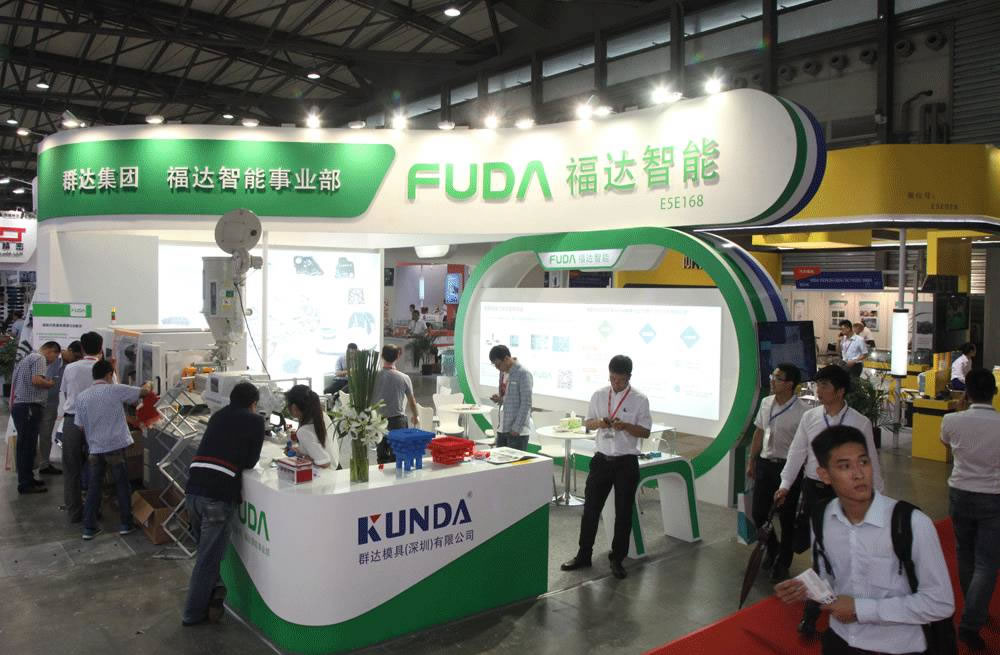
江苏泽恩汽车部品制造有限公司开发的博世高压电喷系统部件注塑模具,用于生产高压电喷系统的喷油嘴零件,采用KISTLER 压力传感器对模具型腔压力进行可视化监控,产品合格率达到99.95%,达到德国同类模具水平。
浙江赛豪实业有限公司开发的精密汽车双色底座模具,制品由两个塑料制件组成,制件接合面需采用激光焊接,形状吻合度要求高,通过模具型腔压力监测技术,控制制件变形量,保证了制件良好的装配效果。
2.模具结构的复杂化和柔性化
塑料模具企业不再着眼同质化的低成本模具技术的竞争,而是越来越注重用户的个性化与复杂高难度需求。如转印定制模具技术、叠层模具、双色双物料模具、高光注塑模具、微发泡工艺模具等,参评的模具结构新颖,工艺成熟,应用也越来越广泛,很好地满足了用户产品的性能要求。
青岛海尔模具有限公司开发的精密转印定制注塑模具,在模内转印技术方面实现了突破,采用创新的膜片夹持吸附结构,实现较深型腔的图案转印和精确的图案定位。采用先进的膜片 3D 数码打印技术,能够为产品用户提供个性化图案的制品。该模具的相关技术已推广应用到洗衣机、空调、冰箱、清洁机器人等产品的外观图案定制领域,产业化效果显著。
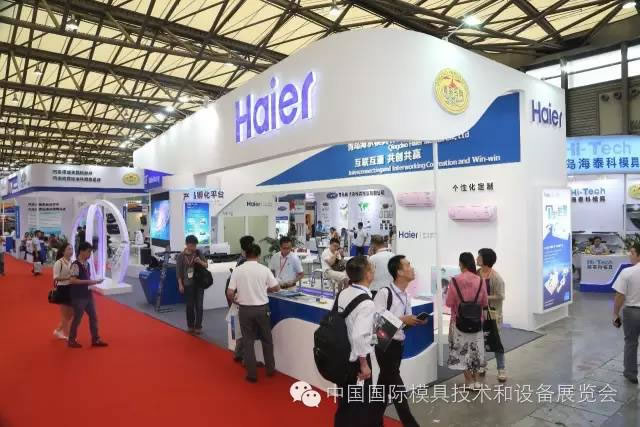
近年来,行业内骨干模具企业在叠层模具、双色双物料模具等新技术方面实现了突破。同时,面向行业开展了技术示范、标准起草等工作,带动新技术在模具行业的推广应用。从本届展会的参评模具来看,部分模具企业已经掌握了这些新型模具技术,并打造成了企业新的增长点。
天津银宝山新科技有限公司开发的大型汽车前保护板叠层注塑模具,属于大型双叠层模具,用于生产汽车前保护板零件,生产效率接近单层模具的两倍,模具使用情况良好,能够满足用户对注塑生产效率、成本、设备利用率的需求,符合高效模具的发展方向。
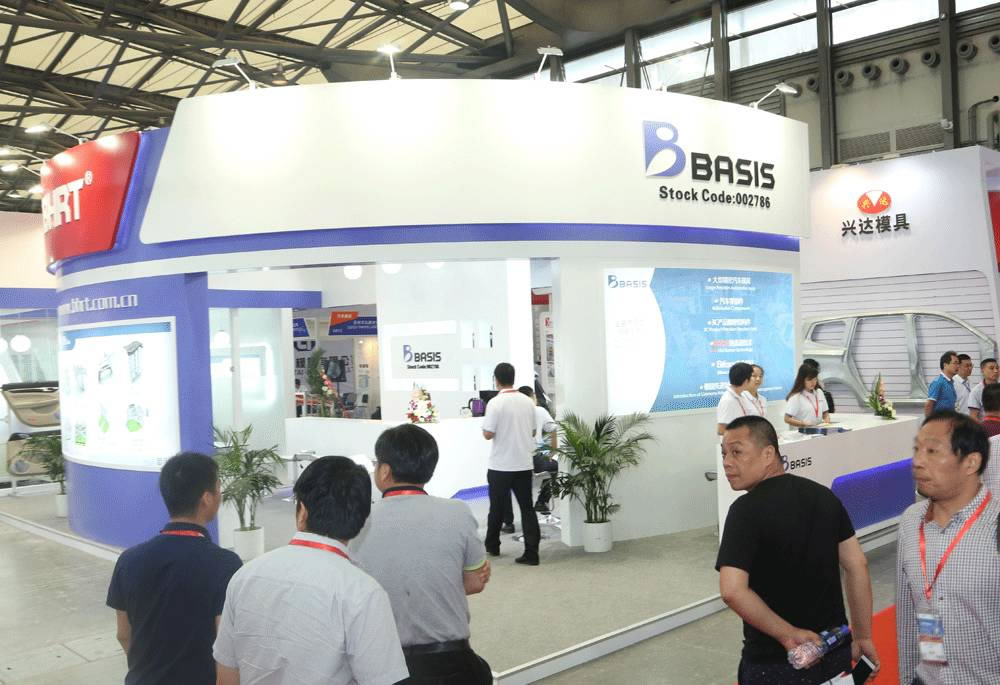
青岛海瑞德模具制品有限公司开发的双色法兰注射模具,所生产的水泵法兰制件由PP+30%GF 和TPE 两种材料组成,尺寸精度和同心度要求高,需满足水压力密封的要求。由于制件的特殊结构,该模具采用创新的滑块式双色注塑模具结构,不仅解决了传统双色模具结构无法解决的 TPE层浇注问题,还辅以精密加工和组装工艺,保证了一模四腔的高精度互换性。同时,结合长轴类零件的精密加工、倒扣形状强脱结构、复杂零件冷却等解决方案,使模具和制件超过国外客户的质量标准,并取得了制件的供货权。
宁波锦隆电器有限公司开发的 DW300 曲线锯外壳模具,采用双色双物料注塑工艺,制件内部形状复杂,制件配合精度要求高,模具分型曲面形状复杂,要求模具的加工研配精度高,实现型腔的精密互换,消除飞边、锐边等引起手感不适的缺陷。软胶为多区域形状,为保证充填质量,采用新颖的多点进料浇口。
高光注塑模具技术已比较成熟,应用也比较广泛,但本届参评模具在加热方式方面又出现了新的创新。四川长虹模塑科技有限公司开发的电视面框电水复合高光注塑模具,用于生产 55 寸电视高光面框,采用电水复合方式完成注射过程中的急冷急热。模具的研制过程中解决了模具急冷急热通道的设计排布;模具急冷急热通道直径及长度的精确加工、加热棒接头处的高温高压密封防止产生蒸汽泄露、电水复合模具的加热系统植入模具内部,加热不需要外围蒸汽、模具加热、冷却与注射过程的联机控制等关键技术。电水复合模具可使模具局部温度分开控制,如分型面需要高的温度,可以将分型面加热棒的加热时间延长以提高其温度;与传统的蒸汽高光模具相比,电水复合模其蒸汽在模具内部产生,能节约 50%的能源费用,提高生产效率 10% ~ 15%,具有节能安全、提升产品质量等优势,同时摆脱了高光模具对外部蒸汽源的依赖。
微发泡工艺在保证制品性能的前提下,可以明显减轻制件重量和成型周期,大大降低设备的锁模力,并具有内应力和翘曲小、平直度高、尺寸稳定等优势,特别是由于微孔尺寸小于材料内部的缺陷,微孔的存在使材料中原有的裂纹尖端钝化,有利于阻止裂纹在应力作用下扩展,从而改善塑料的力学性能。下面两副模具采用微发泡工艺,结合制品的结构进行了创新,获得用户的高度认可。
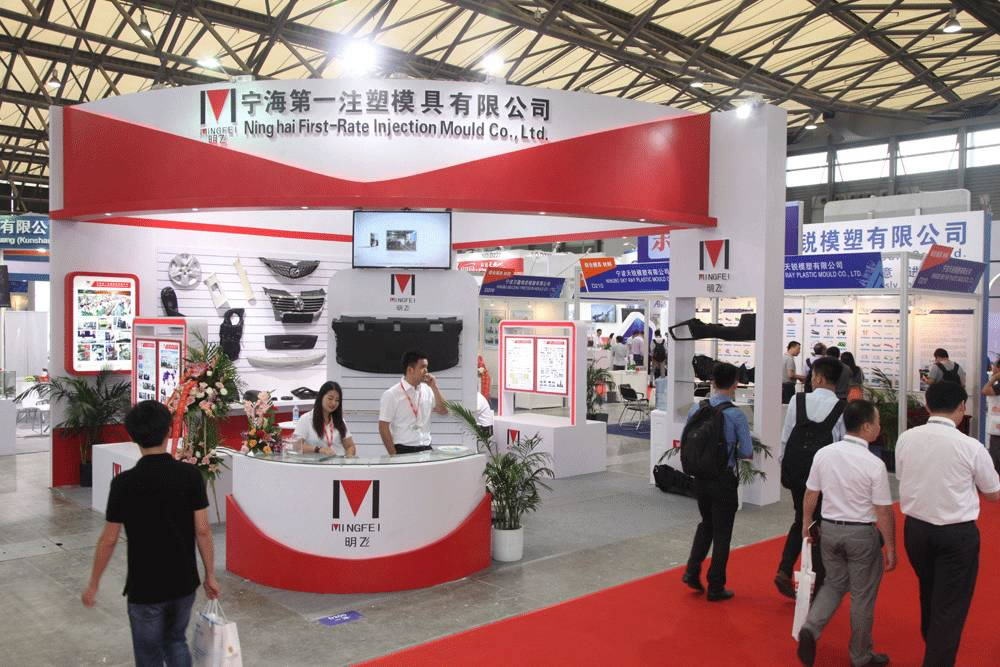
宁海第一注塑模具有限公司开发的大型复杂骨架微发泡注塑模具,用于生产中央通道骨架零件。该模具的研制首先针对微孔发泡的工艺特点,对产品结构设计进行了优化。运用 CAE模流分析,对模具浇注系统的设计方案进行比较论证,运用分析结果优化模具的冷却和排气设计。针对微孔发泡注射成型工艺的要求,抽芯斜顶都精心设计了冷却温控回路,保证模具温度稳定,机构动作可靠顺畅。经验证,模具设计合理,工作可靠,制品微发泡特征良好,泡孔细密均匀,制品减重率在 6% ~ 10% 范围内可调。模具成型周期约 50s内,比传统工艺缩短 20%,翘曲变形明显改善,尺寸和变形均达到客户标准要求。
青岛海泰科模具有限公司开发的微发泡注塑模具,用于生产微发泡工艺的副仪表板骨架零件。该模具设计采用 CAE模流分析,研究了微发泡工艺、浇口等相关参数对气泡大小和密度的影响,针对微发泡模具的鼓包缺陷进行了模具结构优化,避免了制件的鼓包现象,提高了成品率。优化了水路、排气等系统,扩大了微发泡的工艺窗口。
3.模具设计制造趋于精细化
模具的设计与制造更加精细化。模具企业已不再局限于研究产品零件的质量要求,而是更加重视满足产品的质量、性能、成本要求,表现为在传统模具上探索新的模具研制模式和方法,满足或超越产品质量、性能、成本标准,提升企业自身的市场竞争力。
模具及制品精度方面,宁波贝隆精密模塑有限公司开发的车载 HUD 抬头显示模组投影镜筒精密注塑模具,所生产镜筒制件是模组的核心零件,材料为高温尼龙 PA 材料。其上下镜筒的镜片档要求同心轴、圆度、直径大小均控制在 0.01mm 内,产品锁镜片用的螺牙外径与镜片档的同轴度要求控制在0.02mm内,精度要求非常高。该模具的关键技术主要包括两方面,一是高精度加工工艺,如齿轮传动机构的轴承孔选用了超精密坐标磨床加工,精度控制在0.005mm。牙轴的螺纹加工牙形公差要求控制在±0.002mm 以内,材料硬度为 56HRC,选用高精密自动螺纹磨床加工;二是模具脱螺纹机构的创新,采用二次开模一次退牙一次抽芯,配合伺服马达脱螺纹牙轴传动机构,全自动生产,保证了制件螺纹精度和量产的稳定性。厦门唯科模塑科技有限公司开发的10ml 酒精擦拭器注塑模具,所生产的制品为细长薄壁精密医疗用零件,壁厚仅为 1mm,要求壁厚均匀。为了防止注塑过程中,发生盲孔型芯偏移的问题,模具采用细长型芯定位机构,解决了壁厚不均的问题。制件端部的螺纹采用精密脱螺纹机构,通过高精度旋转与移动,保证薄壁件的螺纹能够顺利脱模。
制品变形控制方面,汽车注塑模具的用户对制件变形量提出了很高的要求,采用传统的模具开发方法很难满足用户的需求,部分模具企业已形成解决制件变形问题的有效方案。该方案采用了 CAE模流分析、产品结构优化、预变形设计、试验模具验证、三坐标数据测量、预变形修正等方法,确定制件的最终结构尺寸,然后再进行正式模具的设计与制造。宁波远东制模有限公司开发的FIAT553 汽车行李架支持座注塑模,用于生产汽车行李架支持座零件,以塑代钢,降低成本,满足客户汽车轻量化的需求。制件材料为尼龙加玻纤塑料,材料流动性差,制件长度达1650mm,变形量大,尺寸难以控制,装配贴合面要求高。青岛英联精密模具有限公司开发的“汽车天窗支架模具”,用于生产汽车天窗支架零件,汽车天窗模块需要满足安全性、耐久性、密封性、舒适性等性能指标,所以对天窗支架的尺寸精度提出了很高的要求,制件需要严格控制变形。这两副模具的研制均采用了该方案,极大地降低了模具的质量风险,保证制件质量达到产品标准,大幅提升了模具用户的满意度。
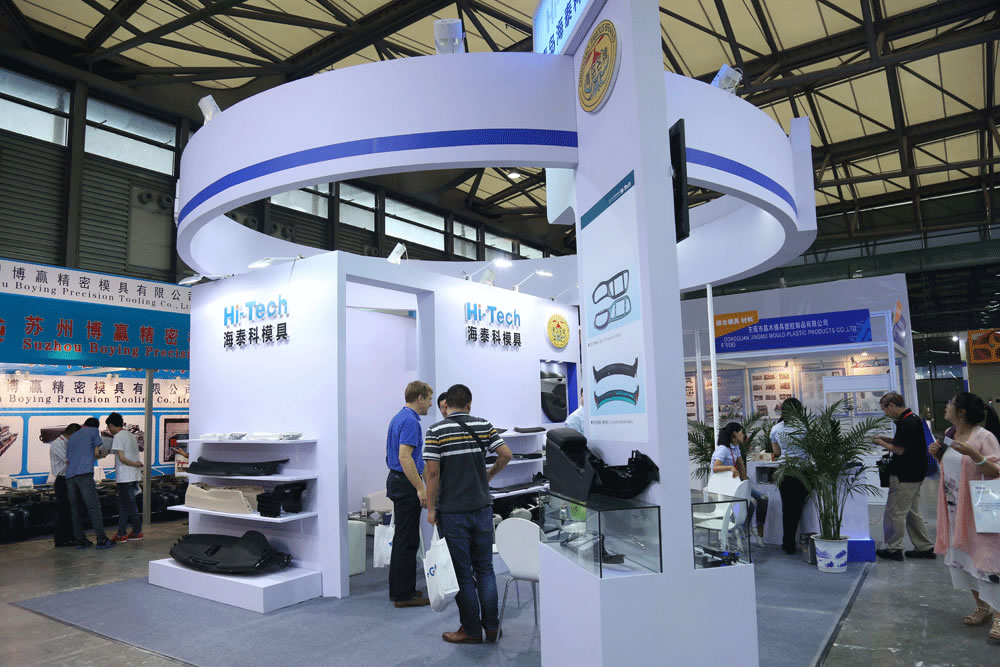
制品强度方面,厦门威迪亚精密模具塑胶有限公司开发的自行车前叉塑料模具 , 所生产制件材料为PA66+40%GF,需要满足抗冲击性和高强度的产品性能要求。该模具属于新型自行车前叉一体成型模具,采用低熔点的易熔型芯(可溶解回收再利用),通过一次注塑得到完整的自行车前叉,各部分间一体成型。同时,可依据产品需求的强度更改易熔型芯的形状,从而达到改善产品强度的要求。相比传统吹塑工艺,没有缝隙和焊接借口,强度好,成型周期短,壁厚均匀,产品尺寸精度高,且外观美观。
降低成本方面,东明兴业科技股份有限公司开发的 HM2X 前壳小型化精密注塑模具,采用模具小型化设计方案,运用堆叠和紧凑排布的设计理念,减小模具的外形尺寸,减小注塑设备规格,从而节约模具和生产成本。运用力学计算分析的方法,校核模具零件的刚强度,保证模具结构的可靠性。模具零件加工采用自动在线检测设备,实现零件加工的自动检测,保证加工精度。该模具总体尺寸比传统模具缩小 40%左右,产品料把重量比传统模具料把重量减少 30% 左右。
提升效率方面,麦迪池杰(厦门)模具科技有限公司开发的 38kV 固封极柱模具,所生产的制品为高压电器元件,成型材料为环氧树脂,模具成型温度为150 ~ 180℃。该模具自带加热系统,模具各零件采用均布分组控制的电加热管和热电偶,通过控制器对加热温度进行精确控制,解决了传统机台加热方式成型零件加热不均匀、产品气泡多、成型周期长等问题。该制品为嵌件注塑,注塑前需要在模具内放置多个金属嵌件,嵌件的安装采用了新颖的整体式嵌件安装桌,嵌件在安装桌上一次安装到位,移动工装一次安装到模具相应位置,大幅度缩短了嵌件的安装时间。
4.模具的新技术水平不断提高
参评的模具企业不再局限于传统模具专业领域,出现了很多高新技术模具。如宁波方正汽车模具有限公司开发的新型汽车油箱吹塑模具,其关键技术包括把原来圆筒形的料坯改为片式料坯,通过中间模把两片料坯分别吸附到模具的两个型腔上,然后吹塑成型。通过中间模辅助在产品吹塑成型过程中直接把功能阀焊到油箱内部,油箱表面无需打孔,解决了油箱汽油渗透的问题。模具在不同区域设计不同大小的排气塞,保证了片式料坯可以均匀地吸附到型腔上。该模具的主要技术参数与国外同类模具比较,碟形机构与燃油箱本体模具装配公差达到 0.05mm,超过国外进口模具 0.05 ~ 0.1mm 的水平,吹塑工艺达到 6 层吹塑,模具价格仅为进口模具的 1/3,其它指标达到国外进口模具水平。所生产的油箱吹塑技术燃料系统的排放量明显低于传统吹塑成型的燃油系统,可以实现油箱重要零部件在油箱成型过程中内置,使油箱渗透性能达到 PZEV 要求,属于塑料燃油箱系统领域目前最先进的技术。
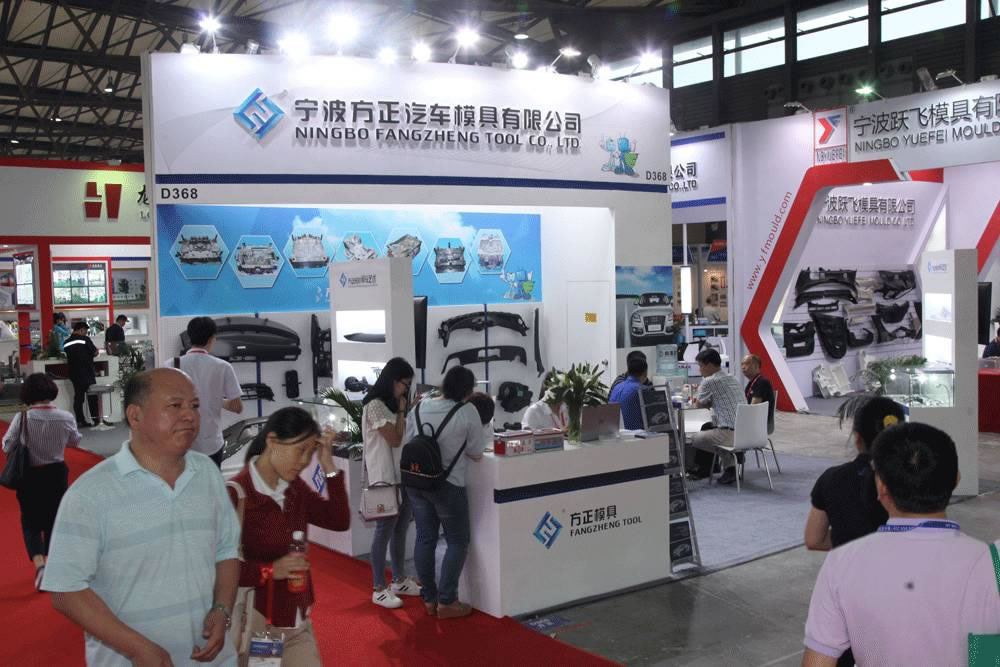
厦门超日精密模具有限公司开发的 G5-397 机架模具,制件为 CPU 水冷散热器的核心部件,服务器的散热、降噪等性能要求模具解决以下问题:陶瓷轴心和机架同轴度和垂直度的高精度,制件脱模困难,在日常高低温使用环境下容易产生蠕变,导致使用寿命下降等。模具采用 CAE 模流分析确定合理浇口形式及位置,保证了充填效果和制件的尺寸精度。轴芯与机架一体成型,陶瓷轴芯在高分子结晶过程中进行融合固定,同轴度达到 0.01mm 以内,蠕变系数小,耐磨损系数高,减少使用过程的磨损量,保证零件的稳定性。模具零件采用 YG20 材质,解决了放置陶瓷轴芯导致的模具磨损而产生的毛边问题。采用双向多级脱模机构,分段顶出,对结晶后的脱模力进行多重分解,保证了机架的平行度和垂直度。为提高塑件结晶效果,模具采用前后模独立的双组加热、双组冷却控温设计,模温均匀,使塑件在成型过程中充分结晶,提高结晶致密性,减小蠕变,提升了尺寸的稳定性。该模具生产的制品使用寿命达到 5 亿次以上。
二、冲压模具篇
本届展会的冲压模具与往届展会相比,无论是模具品种与规模,还是模具技术水平和品质都有新的亮点,盛况空前。标志着冲压模具先进水平的多工位多功能和高效智能化模具发展趋势强劲。展品涵盖了电子、通信、汽车、电机电器、仪器仪表、医疗器械、自动化装备、轨道交通、航空航天、军工机械、新能源和家电等产品领域。从展品的水平分析,模具在复杂程度、结构优化创新、制造精度与粗糙度、使用寿命、性能、技术含量、制品质量和加工周期等方面两年来进步显著。部分国产高档模具在品质和性能上与国外先进模具相比水平相当,不仅替代进口,而且有相当一部分模具出口到工业发达的国家和地区,模具的出口量大幅度增加,模具的国产化程度越来越高。纵观本届参展和申报的模具项目中,冲压模具的特点是:大型复杂级进冲压模具技术进步显著,精密高效长寿命级进模具精品荟萃,多功能自动化模具精彩纷呈,在展会上引起了广大参观者和相关人员的极大关注。
1.大型复杂级进冲压模具技术进步显著
祥鑫科技股份有限公司研制的管道式换热器集液管整体级进成形模具,用于冲制汽车散热器产品。该模具重量 12t,21 工位,8000kN 冲床,模具使用寿命 100 万冲次,冲次 25 次 /min,属大型复杂精密级进模具,产品形状复杂,精度要求高,技术难度大,在一副模具内实现异形复杂双管道式零件的多工位卷圆成形、侧翻成形,扁管槽采用整体冲一次成形和模内自动铆装产品组合一体化功能,特别是一模双列,替代了国外分工序冲压模具。模具结构工艺优化和技术创新显著,获国家专利 3 项,并取得了重大的社会效益和经济效益。该模具已通过中国机械工业联合会科技项目的技术鉴定,模具技术达到国际先进水平。
宁波鸿达电机模具有限公司研制的 Y2-255 芯片套裁大型级进模具,用于工业电机铁芯片产品。该模具长 3m,重量 10t,制造精度 5µm,在 4000kN高速冲床上使用,冲速达 100 冲次 /min,使用寿命5000 万冲次以上。该模具的主要特点是一模多列,套裁和自动化程度高,在一副模具内能同时生产 2P、4P、6P 等不同极数的落料圆片,套裁提高材料利用率5% ~ 10%,一模多列产品输出采用 12 条自动化装置。该模具实现了大步距高速多列套裁和节材等技术(已受理发明专利)。获得宁波市重点工业新产品奖,并通过省市级科技项目的技术鉴定。该项目的技术研发已不仅仅局限于模具制造企业的努力,而是从模具上下游产品、产业链和产业联盟,联合研发提升竞争力。
南通超达装备股份有限公司研制的剪切式地毯•切模具,用于冲制汽车内饰件产品。该模具重量 8t,使用寿命 50 万冲次以上。模具通过结构优化和技术创新,解决了组合导向系统的设计制造关键技术,实现剪切式刀口进行冲切,既提高了导向精度又提高了产品边缘的冲切质量和效率。该模具属大型复杂冲模,形状复杂曲面起伏大,技术难度相当大,创新成效显著,切断率从 90% 提高到 98%,掌握“零间隙”的工艺创新等技术获国家专利 4 项(其中 1 项已受理发明专利)。该模具的技术水平属国内领先水平。
2.精密高效长寿命级进模精品荟萃
厦门特克模具工业有限公司研制的 SOP016L(94×150)-12P 引线框架模具,用于冲制 IC 集成电路产品。该模具属精密高效级进模具,制造精度达1µm,细小凸模数量多达 800 个以上,模具在高速冲床使用,冲速达 400 冲次 /min,使用寿命 5000 万冲次以上。为解决产品尺寸小、腿数多(16 腿)、多排列(12 排)、材料薄(0.23mm)和共面性要求很高在 0.01mm 之内等关键技术,模具结构与工艺进行优化和创新,生产的产品很好地满足用户要求,替代了日本进口模具,并获国家专项 2 项。引线框架是分立器件和集成电路的载体,其主要特点是种类多、数量大、精度高、形状复杂、尺寸细小、材料薄、表面需要局部电镀、外观要求严格。近几年,随着科技的发展,国内高速精密冲压引线框架生产技术有了很大提升,国产模具的技术水平已经接近或达到国外同类模具的先进水平。
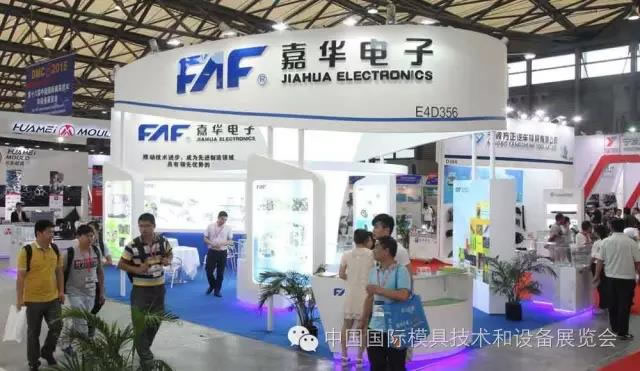
昆山嘉华电子有限公司研制的连接器精密高速级进模具,形状复杂精度要求高。该模具结构优化和精准制造,采用镀氮化处理(PVD)提高超硬合金凸模寿命 2 倍以上。模板深冷处理,上下模座材料采用了高强度高硬度合金铝(A7075),满足了重量轻而强度要求高的需要,实现模具在 300kN 高速冲床上的冲速达 800 次 /min,一次出 16 件产品,使用寿命 3 亿冲次,模具技术水平已达到或接近国外同类模具先进水平,替代了进口模具。
无锡国盛精密模具有限公司、黄山三佳谊华精密机械有限公司等研制的变薄拉伸换热器翅片高效级进模具,具有以下技术特点:
- (1) 模具结构设计功能模块化。根据制品要求,集成众多结构复杂的功能模块于同一模具,并可适当进行柔性化组合,达到三步进和四步进。
- (2) 精度高、设计制造技术难度大。通过采用现代高精密制造工艺技术,关键零件尺寸精度达 1µm,可互换。
- (3) 高速高效。在配套进口高速冲床上使用,冲速达 280 冲次 /min,并实现 60 列三步进或四步进自动送料,完全满足高效规模化生产需求。
- (4) 使用寿命长。采用了 HP40 粉末冶金钢、硬质合金等新型模具材料,刃口件单次刃磨寿命达 3000万冲次以上,模具使用寿命 5 亿冲次以上。
- (5) 技术创新显著。不仅通过对厚度为 0.095mm的铝箔进行多步拉深成型,还对冲孔翻孔后的成型孔再次进行变薄拉深和二次翻边,并采用了多项自主知识产权专利技术,改善了空调换热器的高能效比指标,有利于节能降耗,具有较高推广价值,技术水平与国外同类模具先进水平相当。
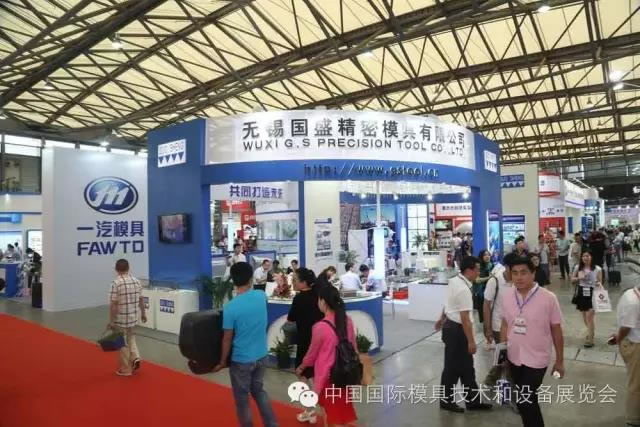
3.多功能自动化模具精彩纷呈
集机电技术为一体的电机铁芯自动叠片级进模具,该模具在高速冲床上使用,具有自动冲压、叠片、扭槽、回转、厚度分组、安全保护和产品输出等功能,模内实现叠铆组装,铁芯组合件厚度达 90mm 以上,计量监控智能化、自动化。本届展会的铁芯自动叠片级进模中有大型铁芯自动叠片,三列铁芯自动叠片、铁芯双回转自动叠片、双列铁芯大回转自动叠片、笔型铁芯自动叠片等展品,给人们留下了深刻印象。如宁波震裕科技股份有限公司研制的笔型点火器铁芯级进模具,用于汽车发动机产品。该模具采用伺服电机驱动精密丝杠进行凸、凹模移动,实现控制凸、凹模在不同位置冲出不同宽度截面,模内叠铆组装和自动出件。采用移动式凸、凹模技术和两组凸模可任意多种片型,解决了由于片型大导致级进模具过长、送料稳定性差等难题。该模具涉及一种非等截面铁芯在级进模具中的冲裁方式,在级进模具中两个工位内实现12 种不同截面铁芯的成形技术,缩短了模具长度,降低了生产成本,获国家发明和实用型专利各 1 项。
厦门捷昕精密科技股份有限公司研制的端子框架双触点自动铆接模具,用于冲制微动轻触开关产品。该模具的特点是在多工位模具上研制了自动输送触点机构,通过输送系统精确定位到料带上进行模内铆接组装成品,并研制了成品切断和气电组合装置,实现了一出 4 件,冲床速度达 150 次 /min,模具使用寿命可达 5000 万冲次以上。该模具通过生产工艺和模具结构创新优化,提高了产品质量和生产效率,解决了原来的单个冲件后,再与触点进行成品铆接,工序繁多、单个生产效率低下、不良率高的生产问题。获国家专利 1 项,创新点突出,替代了进口模具。
宁波美高五金科技有限公司研制的 22F 动簧组合(衔铁及银触点)模内铆接多工位级进模具,用于冲制电磁继电器动簧组合产品。该模具通过结构优化和技术创新,实现了在一副模具内完成动簧片组合的动簧片料带冲制、银触点铆接、动簧片弯曲成形、衔铁铆接等全部工序,大幅度降低了生产成本,提高了品质和生产效率。同时在模具内设计两组防漏铆检测装置,分别检测银触点、衔铁有否漏铆。当有漏铆发生时,检测装置发送冲床传输停机信号,冲床自动停机,有效地控制了漏铆次品的产生,提高了产品合格率。该模具包括了冲压成形和铆装成品一体化技术、银触点及衔铁漏铆检测装置技术,成效显著,模具水平与国外模具水平相当。
成都宏明双新科技股份有限公司研制的屏蔽罩模内装配多工位精密级进模用于冲制屏蔽罩产品。该模具通过结构优化和技术创新,在一副模具内实现两种材料和两种厚度的自动冲压成形和模内组装,冲床速度达 150 次 /min,模具使用寿命预计 6000 万冲次,模具技术水平属国内领先水平。
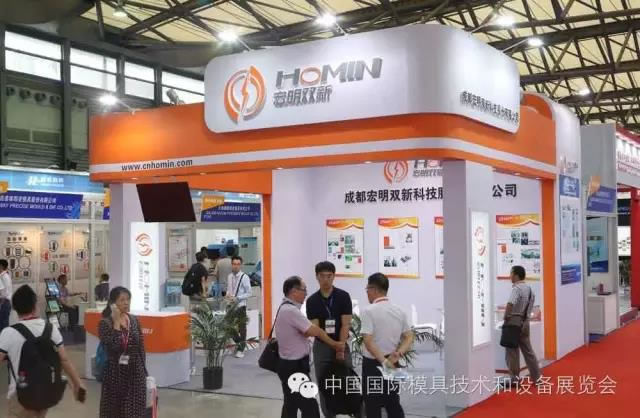
可以预测:随着电子、信息等高新技术的持续发展,以及市场需求的个性化与多样化,未来以高档模具为核心的高效精密冲压技术发展趋势是精密化、高速化、网络化、柔性化、集成化、信息化和智能化、低碳环保及全球化。
(来源:《中国模具信息》杂志)